Discover What is Porosity in Welding and Its Effect on Architectural Stability
Discover What is Porosity in Welding and Its Effect on Architectural Stability
Blog Article
Recognizing Porosity in Welding: Checking Out Causes, Impacts, and Avoidance Techniques
Porosity in welding is a persistent challenge that can dramatically affect the quality and integrity of welds. As specialists in the welding sector are aware, recognizing the causes, impacts, and prevention techniques connected to porosity is critical for attaining durable and trusted welds. By delving into the source of porosity, examining its harmful effects on weld quality, and discovering efficient avoidance approaches, welders can enhance their expertise and skills to create premium welds regularly. The elaborate interplay of aspects adding to porosity needs a comprehensive understanding and an aggressive method to ensure successful welding outcomes.
Usual Root Causes Of Porosity
Porosity in welding is primarily triggered by a combination of elements such as contamination, inappropriate shielding, and insufficient gas coverage during the welding process. Contamination, in the kind of dust, oil, or corrosion on the welding surface area, creates gas pockets when heated, bring about porosity in the weld. Incorrect shielding occurs when the shielding gas, generally used in procedures like MIG and TIG welding, is incapable to completely protect the liquified weld pool from reacting with the bordering air, causing gas entrapment and subsequent porosity. Additionally, poor gas protection, commonly because of inaccurate flow prices or nozzle positioning, can leave parts of the weld unguarded, permitting porosity to create. These variables jointly contribute to the development of spaces within the weld, weakening its honesty and potentially creating architectural issues. Understanding and attending to these usual causes are crucial steps in stopping porosity and making certain the quality and toughness of welded joints.
Impacts on Weld High Quality
The existence of porosity in a weld can considerably endanger the total quality and integrity of the welded joint. Porosity within a weld produces spaces or cavities that weaken the structure, making it more at risk to fracturing, deterioration, and mechanical failing.
In addition, porosity can hinder the efficiency of non-destructive testing (NDT) strategies, making it challenging to identify other flaws or stoppages within the weld. This can result in considerable safety worries, especially in essential applications where the structural stability of the welded parts is critical.

Avoidance Techniques Review
Offered the damaging effect of porosity on weld quality, efficient prevention techniques are crucial to keeping the architectural honesty of welded joints. Additionally, selecting the proper welding specifications, such as voltage, current, and take a trip speed, can aid lessen the threat of porosity formation. By integrating these prevention techniques into welding techniques, the incident of porosity can be substantially reduced, leading to stronger and extra dependable welded joints.
Value of Proper Shielding
Correct protecting in welding plays a crucial function in protecting against atmospheric contamination go to this site and ensuring the stability of welded joints. Protecting gases, such as argon, helium, or a mix of both, are frequently utilized to safeguard the weld swimming pool from responding with elements airborne like oxygen and nitrogen. When these reactive components come into contact with the warm weld swimming pool, they can create porosity, bring about weak welds with lowered mechanical residential or commercial properties.
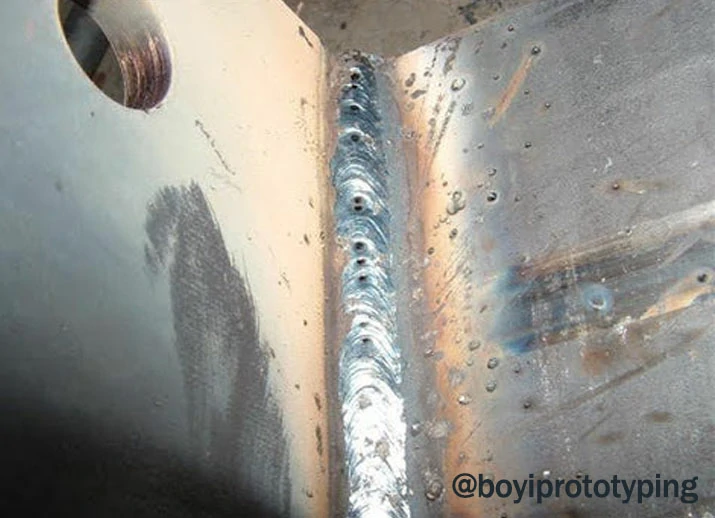
Inadequate securing can result in numerous problems like porosity, spatter, and oxidation, compromising the structural stability of the bonded joint. Consequently, adhering to appropriate securing practices is necessary to generate high-grade welds with very little flaws and make certain the durability and reliability of the welded components (What is Porosity).
Surveillance and Control Approaches
How can welders properly keep an eye on and manage the welding process to make sure optimum results and protect against issues like porosity? By continuously keeping an eye on these variables, welders can recognize deviations from the perfect conditions and make instant modifications to avoid porosity development.

In addition, executing appropriate training programs for welders is important for checking and regulating the welding procedure efficiently. What is Porosity. Educating welders on the relevance of preserving regular parameters, such as correct gas securing and travel speed, can help prevent porosity concerns. Normal assessments this post and certifications can likewise make sure that welders are skilled in tracking and controlling welding processes
Furthermore, using automated welding systems can improve surveillance and control capabilities. These systems can precisely manage welding criteria, lowering the possibility of human mistake and ensuring useful source regular weld quality. By integrating advanced monitoring modern technologies, training programs, and automated systems, welders can properly check and control the welding procedure to minimize porosity issues and attain high-quality welds.
Conclusion
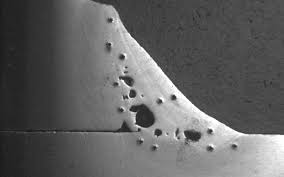
Report this page